Mining companies generate large amounts of waste to produce economically viable metals. For instance, mining for copper, nickel, zinc, and lithium, essential metals for the global push towards decarbonization, can generate an estimated 60 to 90 tonnes of industrial waste, including waste oils and hazardous chemicals, on a monthly basis.
And with ore grades from current operating deposits projected to decrease, miners will need to dig deeper for higher-grade ores to meet production targets, leading to the creation of even more waste and greater logistical challenges.
Consequently, waste management will become increasingly important as companies look to improve performance while also meeting budgets.
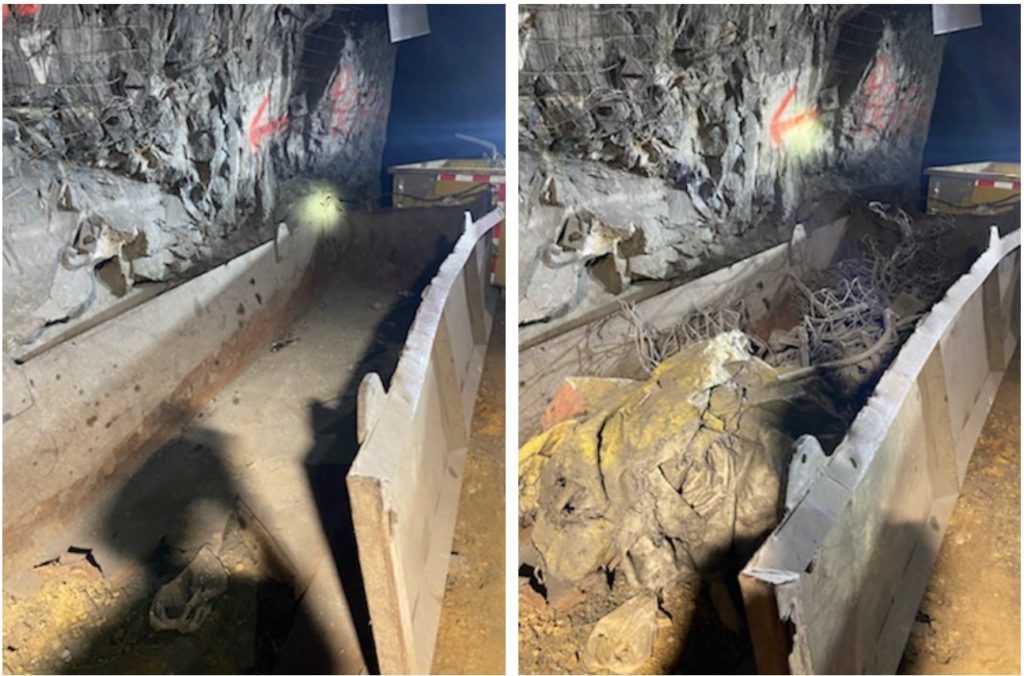
A marked difference before and after A&M crews get to the ore pass bins. A&M Remediation photos
Paul Thususka, president of A&M Remediation, says that mining operations “need an effective waste management strategy to properly handle domestic and industrial waste that firstly minimizes the volume of waste sent to landfill by segregating, reprocessing, or repurposing materials and then responsibly disposing of the remaining waste.”
While acknowledging that case studies on the return on investment (ROI) for good waste management programs are “ambiguous,” he says miners who invest the time and resources into a well-designed waste management program tailored to its needs “can achieve ROIs from 1,000% to over 5,000%.”
Thususka says mining companies that partner with A&M “can achieve savings that go straight to their bottom line through efficiency and productivity improvements, and we’re also passionate about improving the environmental and safety performance of their operations.”
Founded in 2011, the Sudbury, Ont.-based company is a leading specialist in underground waste management at mine sites. For over a decade, it has helped mining companies manage their waste in an environmentally and socially responsible way that improves on-site productivity and creates a safer and better work environment.
“Our approach is to provide a more thoughtful and tailored solution for miners to manage their day-to-day waste management issues, so they can focus on running their operations,” explains Thususka, who has over 30 years of experience in the industrial fields of forestry and mining, where he focused on logistics and waste management.
He notes that although the benefits of a well-designed and implemented waste management program are known by the mining industry, confusion remains amongst the leadership of mining companies over exactly what on-site waste management looks like, what the benefits are that arise from one, and how expenditures in good waste management practices can be justified.
“Even a seemingly inconsequential action such as enabling additional skip loads of ore per day can lead to productivity enhancements for an underground mining operation,” he says.
Such programs, he adds, often “eclipse the investment required to design and implement them,” noting for example that a single mine site can achieve a potential annualized return of over $11.4 million by investing in a robust and sustainable waste management program.
Thususka says that achieving returns of these or similar magnitudes, however, depends on the waste management methods companies employ, their understanding of sustainable waste management practices, and how committed the company, especially the leadership and senior management, are to the process.
Whether “it’s re-thinking how waste from day-to-day activities can be handled better, how scrap metals could be recycled or repurposed, or how hazardous materials are prevented from contaminating ground waters, mining companies can benefit greatly from improved waste management practices,” he says.
For instance, A&M helped Brazilian miner Vale (NYSE: VALE), one of the world’s largest producers of iron ore, to prevent scrap metal from entering the muck circuit at one of its mines near Sudbury, minimizing interruptions to the operation’s ore management.
“From the start of our operation, A&M has been an integral part of our waste management strategy, exceeding all of our environmental targets while increasing our potential to maximize productivity,” says David Kolari, Vale’s integrated operations superintendent at Totten mine, part of the company’s integrated Ontario operations.
Thususka says that even small to mid-sized operations can potentially “save thousands of hours of production time and generate significant cost-savings by freeing up the time an operator spends managing domestic and industrial waste, scrap steel, and collecting garbage.”
A well-designed waste management program also improves the mine site’s environmental performance, he adds.
“Not having to move as many of your large yard bins reduces the number of trips haul trucks have to make, which lowers the operation’s carbon footprint, creating an environmental benefit that can help support better relations with local communities and the company’s ESG [environmental, social, and governance] programs.”
Thususka says that mining operations generate complex waste streams containing “everything you might see on an industrial site,” including food and domestic waste, metals, wood, wastewater, resins, plastics, and paints, as well as a range of hazardous wastes such as oils and acids.
He noted, for example, that A&M has prevented over 120,000 litres of waste oil from entering groundwater over the last 10 years by implementing effective waste oil management on mine sites.
By taking a proactive approach to waste management, which involves “doing it right from the start of a mining operation rather than trying to clean up a site at the end,” he says mining companies can realize “thousands or even millions of dollars in savings as well as increases in operational efficiency and productivity.”
The preceding Joint-Venture Article is PROMOTED CONTENT sponsored by A&M REMEDIATION and produced in cooperation with The Northern Miner. Visit www.amremediation.com for more information.
An effective and profitable strategy to handle mine tailings can be seen in the 2022 SME “Tailings Management Handbook, A Life Cycle Approach”, Edited by VP Kim Morrison, Senior Director, Global Tailings Management, at Newmont. See the case study, “Repurposing Tailings and Other Earth Waste into Ceramics”, by Ross Guenther of Ceramext, LLC.