The world’s biggest miners have been deploying Sandvik’s Remote Monitoring Service (RMS) for fleets of trucks, loaders and drills at underground operations around the world for years.
RMS is a predictive maintenance service Sandvik provides that remotely monitors and analyzes telemetry data from equipment fleets. RMS can effectively identify abnormalities, determine root causes and provide actionable information to eliminate defects.
All this ultimately increases equipment uptime and utilization.
Until now, the services only existed on underground mining equipment, but the global engineering group is rolling out RMS to its surface equipment, including rotary and boom surface drills.
Esa Matilla, Sandvik’s Digital Services Portfolio Manager says the company continues to unlock the value of data by expanding RMS to surface mining.
“Remote Monitoring Service strengthens the partnership between us and our customers. We work collaboratively to drive continuous improvements and maximize the potential of the Sandvik fleet,” Matilla says.
R&D leads to rapid growth
Chris Ewing, Sandvik’s Digital Services Manager, US, notes that while Sandvik’s history is rooted in underground mining, much of the technology has migrated to other areas, namely to surface drilling.
“Now we have capabilities to do open pit and surface mining,” Ewing says. “We’ve had a lot of rapid growth and adoption, particularly in the U.S. The focus has now shifted to expand those service offerings on the surface machines.”
Ewing adds that through the research and development (R&D) process, the US team has seen quick growth and adoption by the market.
Combined with a global pool of reference data and Sandvik’s in-depth analytic skills, RMS can help miners achieve increased productivity with lower emissions, while extending equipment and component life.
Intelligent technology evolves
Remote Monitoring Services started in 2020 with one site in West Africa with 40 machines. Today, there are over 1,600 machines covered under the services by Sandvik, across 125 sites, spanning the globe – and that number continues to grow.
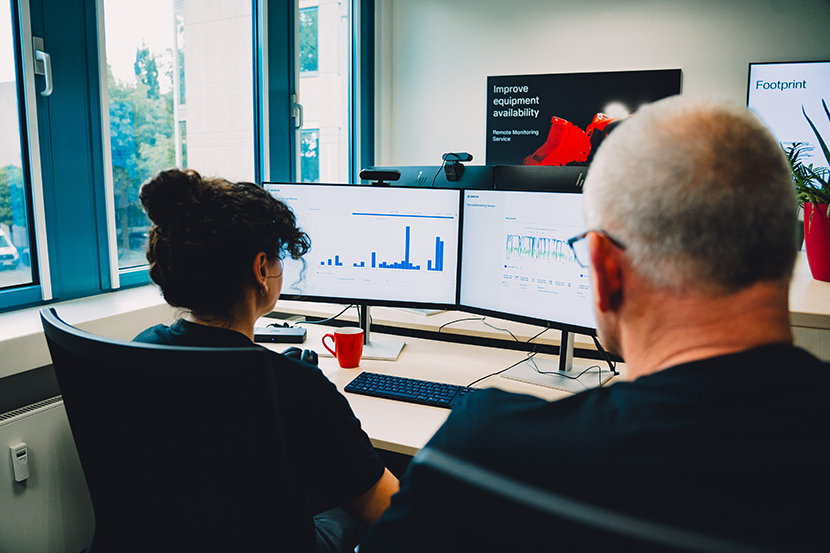
RMS analytics monitoring. Image: Sandvik.
Performance has improved with RMS analytics monitoring, alerting customers as to when maintenance is required, or training is needed to avoid unnecessary downtime, the Remote Monitoring scope has extended to include surface machines – and it all started with a customer fleet of DR410i rotary rigs in the United States.
“Based on that successful trial and the benefits experienced, this customer opted to proceed with the services and expanded the scope to include their DI650i boom surface drill fleet,” Ewing says.
Sandvik has rolled out remote monitoring for rotary blast hole drill rigs, as well as remote monitoring on DI650I boom surface drill rigs.
The remote monitoring service technology followed the same path that automation followed after years of being proven underground.
Leveraging global networks
At sites where RMS is deployed, data becomes a central point of many of the discussions.
Sandvik is able to leverage its global network of product masters, factory engineers, data scientists, and monitoring specialists to work as a force multiplier to quickly detect and respond to new deviations in condition and provide additional insight to more complex issues.
Ewing notes that case studies have shown a variety of predictive insights and proactive recommendations made that have resulted in early intervention that helped either avoid failure completely or gave enough advanced notice to allow for scheduling of maintenance or inspection to reduce downtime caused by unexpected catastrophic failure.
“From electrical shorts and sensor failures to compressor overheating and injector failures we have been able to proactively notify the customer of failure modes before onboard control systems have even indicated issues or fault states,” Ewing says.
“One of the benefits of RMS is that we are monitoring the entire machine as a whole system, not just a focus on any one component. These are complex machines which have several components interdependent on each other and having an in-depth understanding of how they affect each other allows us to derive extremely valuable insights.”
The domain expertise across the different roles involved with the service enables Sandvik an understanding of the machines, their components, and associated data that AI is not easily able to do alone. It’s the people that make AI work – as a tool wielded by Sandvik’s global pool of data experts.
“With our AI and machine learning based tools, we have been able to identify trends that other systems simply would not even catch,” Ewing says.
“We’ve seen our technicians truly start to see the services as a tool in their toolbox to aid in troubleshooting just as our customers see it as a tool in their toolbox to help reduce downtime, decrease troubleshooting time and improve performance.
“The feedback has been overwhelmingly positive so far and the service continues to grow in its capabilities,” Ewing says.
“We are only beginning to scratch the surface when it comes to the value that Sandvik’s Remote Monitoring Services adds to keeping our customers’ machines running at their full potential.”
The preceding Joint Venture Article is PROMOTED CONTENT sponsored by Sandvik and produced in co-operation with The Northern Miner. Visit: Sandvik for more information.
Be the first to comment on "JV article: Sandvik’s remote monitoring service technology expands to open-pit surface equipment"